From manual gages to robotic calipers: How innovation has improved repeatability, reproducibility, throughput, and job satisfaction
More than 60 years ago, the first factory robot started a wave of manufacturing automation. Just 12 years ago, the first commercial collaborative robot brought the benefits of industrial robotics to high-mix, small-batch manufacturing.
As automation technology has advanced, so has the complexity of problems to be solved. Yet some of the simplest challenges continue to confound and frustrate manufacturers. Among these is the challenge of automating measurement of small parts for quality assurance (QA) and quality control (QC).
This white paper explores the evolution of QC measurement techniques, including recent innovations in end-of-arm tooling that allow collaborative robots to perform QC measurements. Like their counterparts in production, collaborative robots in QC automate dull and repetitive work, keep humans safe from injury, and deliver more consistent performance. They improve measurement repeatability and reproducibility as well. With these innovations, collaborative robots give manufacturers a new competitive advantage in the race to maintain high quality and reduce costs.
OR CONTINUE READING BELOW
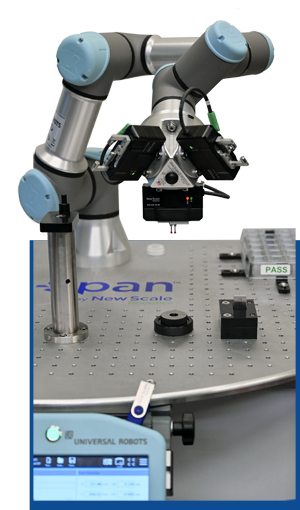
From Fixed Industrial Robots to Collaborative Robots, and From Production to QC
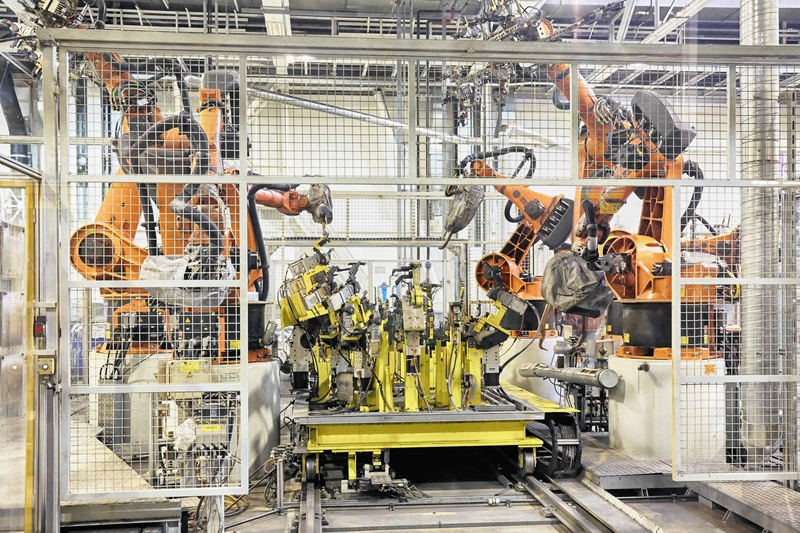
“Fixed” industrial robots often have large footprints, require safety cages, and take 8-10 years for a return on investment (ROI).
Since the first industrial robot launched in 1959,[i] industrial robots for manufacturing have become commonplace in in almost every industry. But for all the benefits they deliver in efficiency and cost savings, these traditional “fixed” industrial robots have some significant drawbacks:
- Installation often requires expensive renovations, due to the large footprint and the need for safety cages to protect nearby workers.
- They cannot be easily relocated, nor easily reprogrammed for different tasks. Software upgrades or repairs may halt production for days.
- With return on investment (ROI) of 8-10 years, advances in technology can render the robot obsolete before ROI has been achieved.
- The skillset needed to operate and repair them requires technical expertise and advanced education. This means few opportunities for workers to retrain or advance as their jobs are changed by automation.
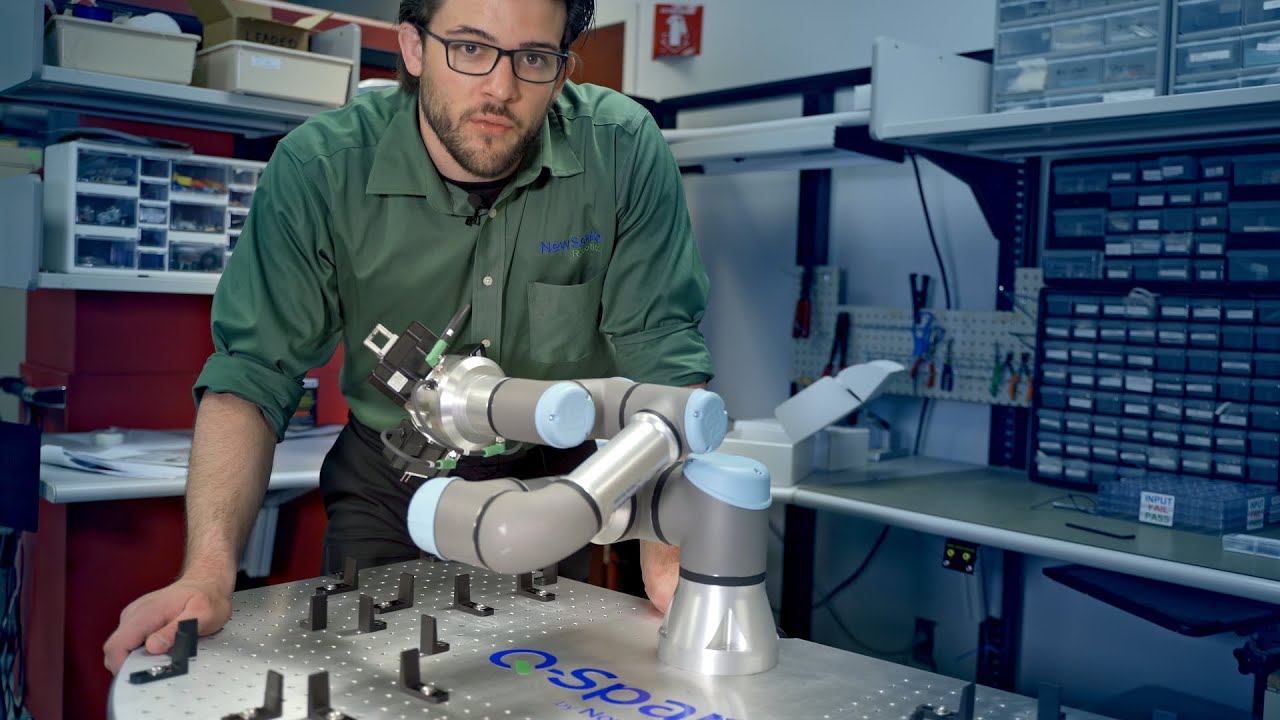
Collaborative robots are smaller industrial robots designed to work in tandem with humans. They have a typical return on investment of less than one year.
Collaborative robots (cobots) were introduced to manufacturing in 2008. They mitigate many of the drawbacks of traditional industrial robots:
- Cobots are designed to work in tandem with human workers.
- Cobots occupy a much smaller footprint on the factory floor and require little to no specialized safety equipment or cages.
- Cobots have a typical ROI of less than year.
- Cobots can be programmed and reprogrammed quickly with a tablet, laptop or “teach pendant.” Workers familiar with a smartphone can learn to program a cobot. This means more opportunity for up-training and advancement for existing employees.
Two key features of cobots are (1) the availability of standard, plug-and-play end of arm tooling for different tasks, and (2) the ease with which they can be “taught” to perform these tasks.
Numerous vendors have developed end of arm tooling for cobots from Universal Robots (UR), the leader in collaborative robots. These tools include electric grippers, pneumatic grippers, screwdrivers, and tools for sanding, cutting, welding and more.
Now a new type of tooling – a precision robotic caliper – extends the applicability of UR cobots to the task of sorting and measuring small parts for quality control.
Evolution of Small-Part QC Measurement
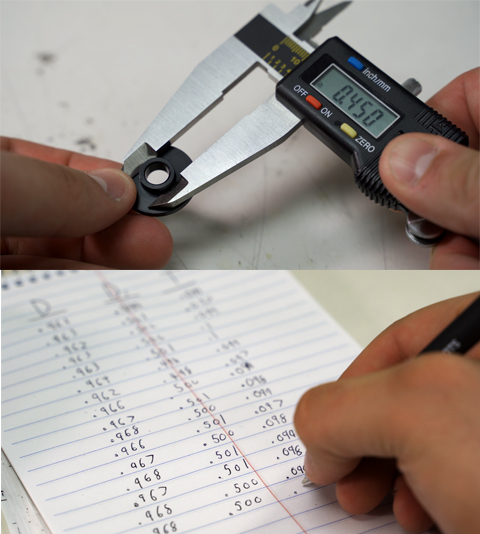
Manual digital calipers depend on operator skill or “finesse” and thus have significant variability over time, and among different operators. Manual data entry is another source of error.
Prior to the Industrial Revolution, factory owners made their own machines for manufacturing. They could make custom parts for their machines as needed. By the 18th century, increasing mechanization required more uniform replacement parts and standardized measurement became the norm.[ii]
Gauges, calipers and micrometers
As mass production became more prevalent, so did the need to produce parts with consistent dimensions, within established tolerances. Thus began widespread use of comparative gauges and measuring tools for QC/QA in manufacturing.
The most common measuring tools – handheld calipers and micrometers – require operator skill or “finesse” to position the tool and part together and interpret the results. For QC inspection of a large number of parts, using manual calipers is tedious at best and may present a risk of repetitive motion stress injury. Measurements vary among operators, as all technicians have different skill levels, experience, and technique. Measurements also over vary time for each individual operator, due to skills development, fatigue, distraction, health, mood and other human factors.
Manual data entry is another source of error. A recent survey of 260 manufacturers—including some of the world’s largest manufacturing organizations— revealed that 75% are still collecting data manually. Of these, an astounding 47% still rely on pencil and paper.[iii]
Handheld “smart” gages are able to transmit data electronically to a computer, which helps to reduce these errors and provides better records for statistical process analysis.[iv] But the problem of human variability in the measurement technique remains.
75% of manufacturers—including some of the world’s largest—still collect QC measurement data manually. Of these, 47% still rely on pencil and paper.
Machine vision and laser-based scanners
The 1970s saw breakthroughs in sensors, machine vision, machine learning and laser-based scanning systems. These advances were applied to meet the demand for higher precision and tighter tolerances on parts. For the first time, a machine rather than a human was responsible for accuracy and measurement.
Machine vision and laser-based scanning are optical measurements that depend on the reflective and transmissive properties of the part being measured and the properties of the lighting source. Shiny surfaces and small surface variations can create false errors in acceptable parts or mask real defects. Laser scanning systems have an embedded light sources but require a consistent surface reflectivity, and may not measure small features with an occluded line of sight.
The art of machine vision requires an experienced engineer to optimize and validate each measurement. Often, only computer technicians or engineers have the requisite expertise, which means opportunities for advancement from the shop floor are limited for workers who do not have post-secondary education in the right areas.
The advantages of optical measurements overcome their limitations, and the applications are growing. Non-contact optical measurement is a good choice for small, thin and fragile parts that cannot be measured with contact instruments. It is also useful for fast in-line inspection. Thin parts with back lighting are ideal for 2D machine vision measurements with micrometer precision. Laser scanners can quickly make 3D measurements of large parts with complex shapes with 100 micrometer precision.
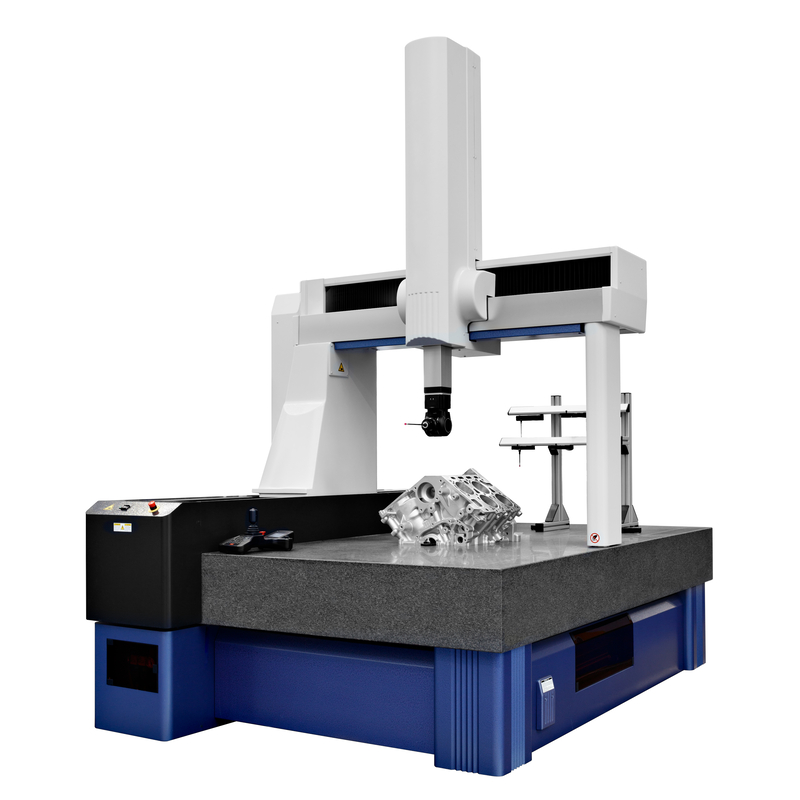
CMM systems perform crucial and complex 3D measurements and are often used for detailed “first article” inspections. They are large and expensive, and require significant training to operate.
Coordinate Measuring Machines (CMM)
The first Coordinate Measuring Machine (CMM) was a two-axis device developed by the Ferranti Company in the 1950s. The first three-axis CMM appeared in the early 1960s. It consisted of 3D tracing devices with a simple digital readout displaying XYZ position. Today’s CMMs evolved from this device.
CMMs measure the geometric properties of an item to precise specifications and can be used either manually, or via computer program.[v] Among the first industrial robots that can be programmed to measure similar objects repeatedly, they quickly became the new standard for quality assurance in small-part measurement. They can generate real-time reports of deviations and risk tolerance fails.
CMMs are expensive precision instruments that require heavy and stiff structures to achieve their fundamental precision. They are not easily relocated once installed. Significant training is required to program each part and collect measurements. Frequent computer and software upgrades and re-training are needed to remain compatible with the newest CAD/CAM programs and avoid obsolescence.
They are susceptible to measurement errors due to moisture and temperature variations and vibration and must be in an environmentally-controlled room. Finally, each part must have unique fixturing and must be inserted and removed by a person. Cycle time for each part is typically several minutes which is not a fit for high-volume manufacturing.
CMM systems are the best choice for making critical and complex 3D measurements of parts with micrometer precision. In high-volume manufacturing they make detailed “first article” inspections that validate a process and certify “golden parts” that may be used for faster in-line comparative measurements.
Enter the Robots for QC
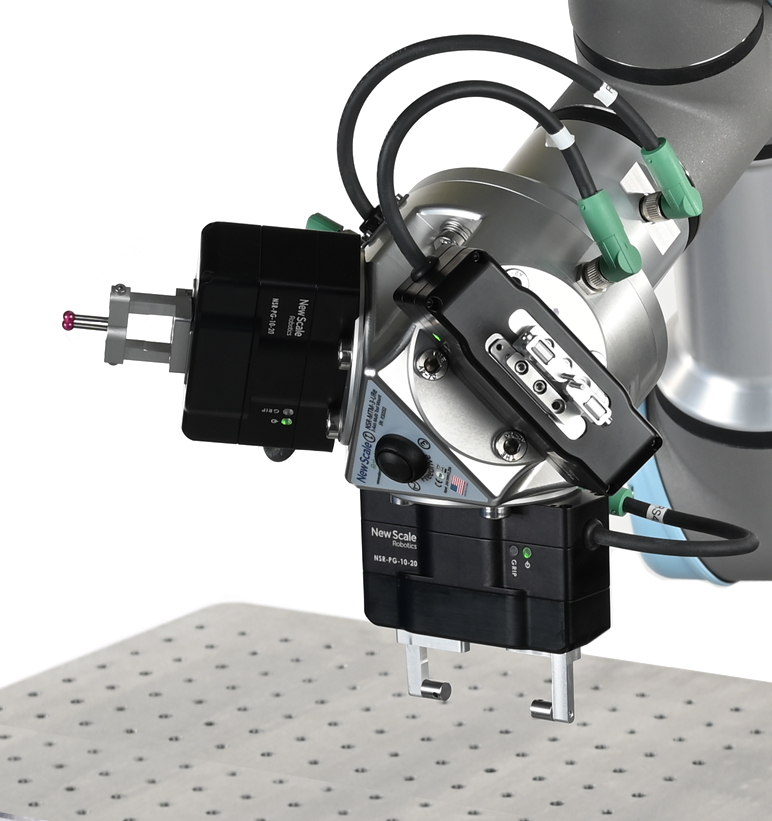
Innovations for cobots support QC measurement: Precision robotic calipers ALSO function as small, lightweight grippers. Here, three are mounted on a single UR3e cobot arm using an innovative mount and software to control picking, measuring, data recording, and placing.
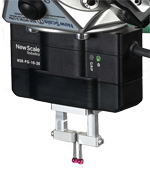
The gripper / robotic caliper of a Q-Span System replaces a manual digital caliper and has about twice the precision.
Just as collaborative robots (cobots) brought the benefits of robotic automation to small-batch, high-mix manufacturing, they are now bringing those same benefits to the QC lab. Three recent innovations have made this possible:
1. Precision robotic calipers
2. Smaller, more lightweight grippers
3. A system that allows multiple calipers and grippers to be mounted on a single cobot, and controlled by a unified program
These innovations support exciting new applications for cobots in the QC lab.
QC robot application 1 – automated small-part measurement
New Scale Robotics has brought these three innovations together and paired them with a UR3e cobot to create a dedicated system for automated small-part QC measurement.
Called the Q-Span™ System, this system can automatically pick parts, measure multiple dimensions on each, and make real-time decisions such as pass/fail based on the results. It can then sort parts into output trays and send all the data to a PC for later analysis.
A typical Q-Span System has one robotic gripper for part handling and one or two robotic calipers to make measurements. In many cases one tool serves as both gripper and caliper. Each caliper is equipped with metrology fingers specific to the part and the dimension to be measured. Dimensions that can be measured include length, width, thickness, outer diameter, and inner diameter.
Three important features of the grippers/calipers are:
(1) their small size,
(2) their light weight, and
(3) the precision of the fingertip motion with position feedback to the robot.
Because they are small and lightweight, three devices can be mounted on Universal Robot’s smallest cobot. This allows the system to occupy minimal lab space, and perform multiple processes with fewer large moves. The result is high throughput and safety for human operators.
The gripper/caliper replaces a manual digital caliper and has about twice the precision. When using the appropriate fingertips and established metrology practices, part measurement resolution is 0.0001 inches (2.5 μm). The +/- 3 sigma repeatability and accuracy are factory-certified to be less than +/- 0.0002 inches (5 μm) and +/- 0.0008 inches (20 μm) respectively.
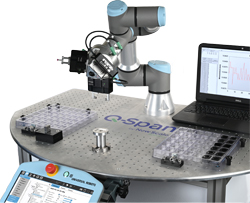
A Q-Span Workstation incorporates gripper/caliper, tool mounting, and software innovations in a robotic solution specific to QC measurement of small parts.
Once the Q-Span System is taught the proper force, position and orientations needed to make precise measurements, it can repeat the procedures indefinitely without fatigue or distraction and can continue to operate in off-hours. It can be taught procedures for many different parts, and then changeover from one part to another can be accomplished in under an hour.
Training and operation are straightforward and do not require advanced technical skills or education. This provides new opportunities for existing QC technicians to advance and receive up-training. The chance to do higher-level work with less tedium helps companies retain valuable employees.
Based on labor savings alone, a Q-Span Solution with Universal Robot installation has an average ROI of less than 11 months. The ROI is faster when considering the ability to add QC capacity without increasing headcount.
New Scale Robotics provides a free application study and assessment of a manufacturer’s first part before any investment is needed.
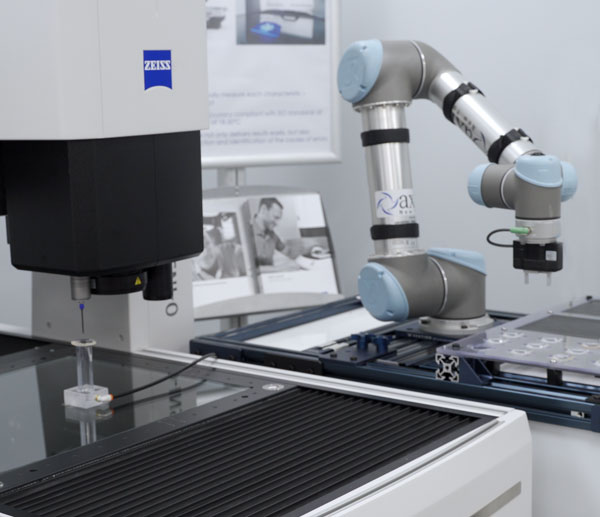
A Q-Span System enables “smart” machine tending of a CMM. A single gripper/caliper makes preliminary measurements of parts before placing them in the machine.
QC robot application 2 – machine tending for CMMs
A cobot be used for machine tending of CMMs. For example, OptiPro Systems demonstrates use of a Q-Span System to automatically load and unload a CMM.
This Q-Span System is configured with one robotic caliper tool that both picks and measures the part. The caliper measurements are used to increase throughput and utilization of the CMM.
If the preliminary diameter measurement is within range, the Q-Span System loads the part into the CMM. If it is out of range, the Q-Span System can place the part directly into a “fail” output tray, and avoid wasting CMM cycles.
After a part is loaded, the CMM uses the Q-Span System’s measurement to determine which routine to perform. It runs its full routine and sends its data back to the Q-Span System, which unloads the part and places it into the appropriate output tray (pass/fail).
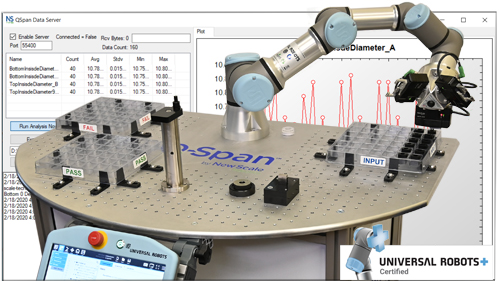
Q-Span Workstations are expandable to include complementary measuring instruments and tools with greater precision.
Robotic tools replace manual digital calipers and other gages
Real-world metrology must measure parts that are complex and it is rare that digital caliper measurements are sufficient to measure all features. Q-Span Workstations are expandable to include complementary measuring instruments and tools with greater precision.
A Q-Span Workstation can incorporate other gages, with digital output, that measure a variety of part features including height, depth, outside diameter, and inside diameter. Examples of complementary instruments and tools include LVDT height gages, laser height gages, 2D laser scanners, air gages, and mechanical snap gages.
Benefits of collaborative robots for automation in QC
Using robots to automate measurements eliminates human variation and reduces delays, scrapped material and cost. Using collaborative robot system architecture insures maximum flexibility for high-mix, small-batch manufacturing. The result is greater inspection capacity and throughput while increasing employee engagement, skills, and retention.
Conclusion
Industrial robots have become a mainstream component of the manufacturing sector, performing tasks that require accuracy, precision and consistency. They are also expensive, require a large footprint on the factory floor, and can rarely be retrofit to existing assembly lines. In addition, they need specialized programming and operation, and extensive safety protocols to operate with human workers in the same environment. Technological advances can render the robots obsolete before ROI is achieved.
Collaborative robots, on the other hand, have sensors and safety protocols to allow them to work in smaller spaces beside human workers. Application-based programming can be updated easily, with little downtime, and the cobot can be programmed by anyone familiar with smartphone application technology. They are easily moved from one location to another and do not require extensive renovations. Existing employees can be uptrained to operate the cobots, providing new opportunities for advancement and employee engagement.
Innovations in end of arm tooling for collaborative robots – including the introduction of small, precise and lightweight robotic calipers – is now bringing the benefits of cobots into the QC lab. The Q-Span System from New Scale Robotics automates small-part measurements, relieving human operators from this tedious manual task while improving repeatability and reliability.
References
[i] Joseph Engelberger, The Father of Robotics. https://www.robotics.org/joseph-engelberger/about.cfm
[ii] The History of Measurements, by MTI Instruments. https://www.mtiinstruments.com/knowledge-center/history-of-measurements/
[iii] Manual Data Collection Delays Digital Transformation for Manufacturers, by InfinityQS, Quality Magazine, April 13, 2020. https://www.qualitymag.com/articles/96029-manual-data-collection-delays-digital-transformation-for-manufacturers
[iv] Choosing the Right Smart Handheld Gage, by George Schuetz, Quality Magazine, March 1, 2020. https://www.qualitymag.com/articles/95292-choosing-the-right-smart-handheld-gage
[v] A History of Metrology – A look at measurement solutions and metrology devices from Galileo to today’s optical systems, by Daniel Brown, Design Engineering, October 3, 2016. https://www.design-engineering.com/features/metrology-1004024832/